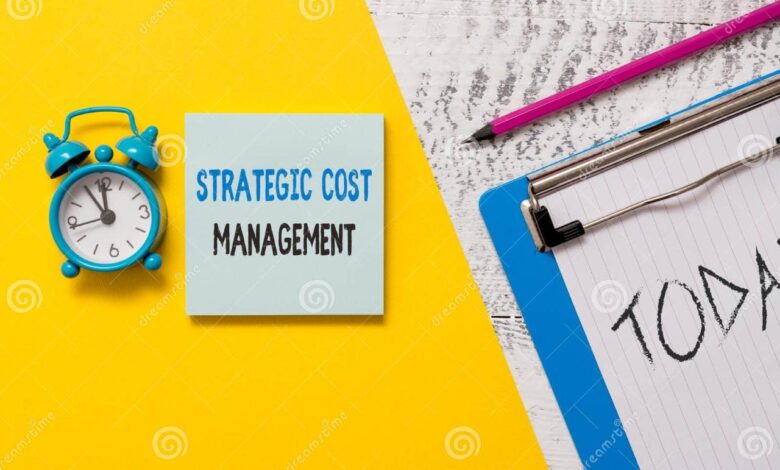
Strategic Cost Management Reducing Expenses Effectively
Strategic cost management reducing expenses is crucial for any business seeking to thrive in today’s competitive landscape. This involves a comprehensive approach that goes beyond simply cutting costs; it’s about optimizing operations and resource allocation to achieve sustainable profitability.
This exploration dives deep into the principles of strategic cost management, offering practical insights and actionable strategies for identifying and implementing cost reduction opportunities across various business functions. From supply chain optimization to technology adoption, we’ll cover a spectrum of techniques, examining their effectiveness and potential pitfalls.
Defining Strategic Cost Management: Strategic Cost Management Reducing Expenses
Strategic cost management is a crucial aspect of modern business operations, moving beyond the traditional focus on simply tracking costs to proactively influencing them. It’s a holistic approach that integrates cost considerations into the very fabric of strategic decision-making, enabling organizations to achieve a competitive edge by optimizing resource allocation and value creation. This proactive management system extends beyond accounting to encompass the entire value chain, recognizing that cost savings aren’t just about reducing expenses, but also about improving efficiency, innovation, and ultimately, profitability.Strategic cost management is not just about cutting costs; it’s about strategically managing costs throughout the entire value chain to achieve sustainable competitive advantage.
This involves a profound understanding of how costs are incurred, and how they can be reduced or avoided in the long term. This approach goes beyond short-term cost reductions and aims for a long-term perspective, where cost management is an integral part of the organization’s overall strategy.
Core Principles of Strategic Cost Management
Strategic cost management is founded on several key principles. It emphasizes a proactive, rather than reactive, approach to cost management. It also emphasizes the interconnectedness of different functions and departments within an organization, understanding that cost reductions in one area may have unintended consequences in another. Furthermore, it requires a long-term perspective, recognizing that short-term cost-cutting measures can sometimes hinder long-term profitability.
Finally, it stresses the importance of continuous improvement, recognizing that cost reduction is an ongoing process, not a one-time event.
Approaches to Strategic Cost Management
Different approaches to strategic cost management can be employed, each with its own strengths and weaknesses. Activity-based costing (ABC) is a detailed approach that identifies and assigns costs to specific activities, allowing for a more precise understanding of cost drivers. Value engineering focuses on improving product design and manufacturing processes to eliminate unnecessary costs without sacrificing quality. Target costing, on the other hand, sets target costs based on market prices and desired profitability, driving cost reduction efforts throughout the product development cycle.
The effectiveness of each approach depends on the specific industry, the complexity of the organization’s operations, and the specific goals being pursued.
Key Distinctions from Traditional Cost Accounting
Traditional cost accounting primarily focuses on cost accumulation and reporting. Strategic cost management, in contrast, emphasizes cost reduction and control. It considers the entire value chain, integrating cost considerations into the strategic decision-making process. Strategic cost management is proactive, while traditional cost accounting is primarily reactive. Furthermore, strategic cost management is forward-looking, considering future trends and market conditions, whereas traditional cost accounting is largely historical.
Traditional cost accounting focuses on past performance, while strategic cost management focuses on future competitiveness.
Framework for Evaluating Effectiveness
Evaluating the effectiveness of strategic cost management initiatives requires a comprehensive framework. A crucial element is defining clear, measurable goals and objectives. These goals must align with the overall strategic objectives of the organization. Progress towards these goals should be tracked and monitored regularly using key performance indicators (KPIs). These KPIs can include cost reduction percentages, improved efficiency metrics, and enhanced profitability figures.
Regular reviews and adjustments to the strategy are essential to ensure ongoing effectiveness and alignment with changing market conditions. Finally, feedback from employees and stakeholders is crucial in identifying areas for improvement and refining the approach over time.
Identifying Cost Reduction Opportunities
Unveiling hidden cost-saving potential within a business requires a proactive and strategic approach. Simply slashing expenses without understanding the underlying drivers can lead to short-term gains at the expense of long-term sustainability. This section delves into identifying areas ripe for cost reduction, analyzing spending patterns, and considering the long-term ramifications of any implemented strategies.Analyzing current spending patterns across departments is crucial for pinpointing areas where expenses can be optimized.
This involves a detailed examination of historical data, comparing costs across different periods and departments. A structured approach to this analysis allows for the identification of trends and anomalies that can highlight potential areas for cost reduction.
Supply Chain Cost Reduction
Optimizing the supply chain is a significant avenue for cost reduction. This involves evaluating procurement strategies, negotiating better deals with suppliers, and exploring alternative sourcing options. Analyzing transportation costs, inventory management practices, and warehousing expenses can reveal opportunities for significant savings. Implementing a lean supply chain, with reduced lead times and minimized inventory, can dramatically reduce costs.
Manufacturing Cost Reduction
Manufacturing processes offer numerous potential cost-saving opportunities. Examining production methods, identifying bottlenecks, and exploring automation possibilities can lead to substantial savings. Utilizing advanced manufacturing techniques, such as lean manufacturing principles, can improve efficiency and reduce waste. A thorough analysis of material usage, energy consumption, and labor costs within the manufacturing department is essential.
Marketing Cost Reduction
Marketing expenses can be scrutinized for inefficiencies. Evaluating the effectiveness of various marketing channels, analyzing campaign ROI, and identifying areas for optimization are crucial. Replacing expensive advertising methods with more cost-effective strategies, like social media marketing or content marketing, can lead to substantial savings. A well-defined marketing strategy that focuses on targeted campaigns and measurable results can drastically improve cost-effectiveness.
Administrative Cost Reduction
Administrative costs often represent a significant portion of overall expenses. Identifying redundancies in administrative procedures, evaluating employee efficiency, and exploring opportunities for automation can yield substantial savings. Reviewing administrative software licenses, office supplies, and other operational costs can uncover avenues for optimization. Implementing efficient workflows and streamlining administrative processes can improve productivity and reduce unnecessary expenses.
Long-Term Implications of Cost Reduction Strategies
When implementing cost reduction strategies, it’s critical to consider the potential long-term implications. While short-term savings are appealing, decisions that jeopardize employee morale, product quality, or customer satisfaction are ultimately unsustainable. Implementing strategies that enhance employee skills, improve product quality, and maintain a positive customer experience should be prioritized. Companies should carefully assess the potential for long-term consequences before making any significant cost-cutting decisions.
Structured Approach to Identifying Cost Savings Opportunities
A structured approach involves a phased process. Firstly, gather comprehensive data on existing processes and costs across all departments. Secondly, analyze this data to identify potential areas for cost reduction. Thirdly, develop and implement specific cost reduction strategies. Finally, monitor the impact of these strategies and make necessary adjustments.
Implementing Cost Reduction Strategies
Turning identified cost reduction opportunities into tangible results requires a strategic implementation plan. This phase focuses on the practical application of chosen strategies, ensuring that cost savings are achieved effectively and sustainably. A well-structured approach is crucial to avoid short-term fixes that may lead to long-term problems.Implementing cost reduction strategies is not a one-size-fits-all process. Successful implementation requires a tailored approach that considers the specific needs and context of each organization.
Understanding the strengths and weaknesses of various methods is essential for selecting the most appropriate tools and techniques for the desired outcome.
Process Improvement Strategies
Process improvement strategies are crucial for streamlining operations and eliminating unnecessary steps. Analyzing current workflows and identifying bottlenecks can reveal areas for improvement. Implementing lean methodologies, such as value stream mapping and 5S, can help optimize processes and reduce waste. This can result in increased efficiency and cost savings by reducing material waste, time spent on unnecessary tasks, and overhead expenses.
For example, a manufacturing company might redesign its assembly line to eliminate redundant steps, resulting in a faster production cycle and reduced labor costs.
Technology Adoption Strategies
Technology plays a significant role in cost reduction. Adopting new technologies, such as automation software and cloud-based services, can streamline operations, improve efficiency, and reduce manual labor costs. Careful evaluation of the return on investment (ROI) is crucial to ensure that the chosen technology aligns with the organization’s strategic goals. For example, a company in the customer service sector could implement a chatbot system to handle routine inquiries, freeing up human agents to focus on complex issues and reduce operational costs.
Outsourcing Strategies
Outsourcing non-core functions can significantly reduce costs. This strategy can free up internal resources to focus on core competencies, while leveraging the expertise and cost-effectiveness of external providers. Choosing the right outsourcing partner is vital to ensure quality and reliability. For instance, a company may outsource its customer support to a specialized call center in a region with lower labor costs.
This could result in significant savings without sacrificing customer service quality.
Obtain direct knowledge about the efficiency of finance departments evolving while bracing for coronavirus second wave through case studies.
Comparing Cost-Cutting Methods
Method | Pros | Cons |
---|---|---|
Automation | Increased efficiency, reduced errors, 24/7 operation | High initial investment, potential job displacement, need for skilled personnel for maintenance |
Vendor Negotiations | Lower prices, better terms, potential for discounts | Requires negotiation skills, risk of losing vendor relationships, potential for quality compromises |
Employee Engagement in Cost Reduction
Employee engagement is essential for successful cost reduction initiatives. Motivated and informed employees are more likely to embrace new processes and contribute ideas for improvement. Communicating the rationale behind cost-cutting measures and involving employees in the decision-making process can foster a sense of ownership and commitment. Creating a culture of continuous improvement, where employees are encouraged to identify and suggest cost-saving opportunities, can yield significant results.
Expand your understanding about how to clearly communicate feedback and expectations with the sources we offer.
Step-by-Step Cost Reduction Initiative
- Define Objectives: Clearly define the goals and desired outcomes of the cost reduction initiative. Set specific, measurable, achievable, relevant, and time-bound (SMART) targets.
- Assess Current Costs: Conduct a comprehensive analysis of current expenses across all departments and functions. Identify areas with high spending.
- Identify Opportunities: Research and analyze potential cost reduction opportunities using various methods, such as process improvement, technology adoption, and outsourcing.
- Develop Strategies: Design specific strategies based on the identified opportunities. Include detailed plans, timelines, and resource allocation.
- Implement Strategies: Execute the developed strategies according to the defined plan. Ensure proper communication and training for employees involved.
- Monitor and Evaluate: Regularly track progress against the defined objectives and make necessary adjustments to the plan. Assess the effectiveness of the implemented strategies.
Measuring and Evaluating Cost Reduction
Successfully implementing cost reduction strategies requires a robust system for measuring and evaluating their impact. Simply slashing costs without understanding the effect on overall performance can be detrimental. This crucial step allows for adjustments, optimization, and ensures the strategies contribute positively to the company’s bottom line.Measuring the effectiveness of cost reduction initiatives necessitates a multi-faceted approach. Different metrics provide varying perspectives on the success of the efforts.
This involves tracking not just the immediate cost savings, but also the broader impact on efficiency, profitability, and operational performance.
Metrics for Measuring Cost Reduction Effectiveness
Various metrics provide a comprehensive view of cost reduction success. A critical aspect is the comparison of pre- and post-implementation data to accurately gauge the effectiveness. Key metrics include:
- Return on Investment (ROI): ROI quantifies the profitability of the cost reduction initiative. It calculates the gain from the investment relative to the cost of the investment. A higher ROI signifies a more successful strategy.
- Cost per Unit: This metric assesses the cost associated with producing a single unit of product or service. A decrease in cost per unit signifies improved efficiency in the production process, and hence, a cost reduction strategy’s efficacy.
- Operational Efficiency: This metric encompasses the productivity and output of various operational processes. An increase in operational efficiency demonstrates that the cost reduction measures have streamlined operations, leading to better output at a lower cost.
- Productivity Improvements: This metric gauges the output generated per unit of input (e.g., labor hours). Increased productivity indicates that the cost reduction strategies have boosted efficiency, which translates to better resource utilization and lower overall costs.
- Cycle Time Reduction: Tracking the time it takes to complete a process from start to finish can reveal whether cost reduction efforts have optimized workflows. Reduced cycle times usually correlate with decreased costs and increased output.
Tracking and Analyzing Cost Reduction Results
Regular monitoring and analysis of cost reduction results are essential for continuous improvement. This process should encompass a comprehensive review of the data to identify trends and patterns.
- Establish Baselines: Before implementing any cost reduction strategy, establish clear baselines for all relevant metrics. This provides a benchmark for evaluating the effectiveness of the strategy.
- Regular Reporting: Develop a system for regularly tracking and reporting cost reduction data. This includes creating a schedule for reporting and clearly defining the data points to be tracked.
- Trend Analysis: Analyze trends in the data to identify any patterns or anomalies. This includes evaluating the impact of external factors (like economic conditions or changes in raw material prices) on cost reduction results.
- Variance Analysis: Analyze the difference between the actual and predicted cost reduction results. This analysis helps pinpoint areas for improvement and allows for corrective action where needed.
- Root Cause Analysis: When variances occur, conduct a thorough root cause analysis to understand the underlying factors driving the deviations. This deep dive helps in proactively addressing the causes and preventing future problems.
Evaluating Impact on Business Performance
The impact of cost reduction strategies extends beyond the immediate savings. A comprehensive evaluation assesses the overall effect on profitability, revenue, and customer satisfaction.
- Profitability Analysis: Assess how cost reduction strategies affect the company’s overall profitability. This includes evaluating the impact on gross profit margin, operating profit margin, and net profit margin.
- Revenue Analysis: Examine how cost reductions affect revenue. Lower costs can potentially lead to price reductions, attracting more customers and boosting revenue.
- Customer Satisfaction: Assess the effect on customer satisfaction. Cost reductions can lead to improved service quality or lower prices, resulting in increased customer satisfaction and loyalty.
Creating a Cost Reduction Dashboard
A well-designed dashboard provides a visual representation of cost reduction data, enabling quick insights and easy comprehension.
- Key Performance Indicators (KPIs): Select key cost reduction KPIs, such as ROI, cost per unit, and operational efficiency. Display these KPIs prominently on the dashboard.
- Trend Charts: Use trend charts to visually represent the progress of cost reduction over time. This allows for easy identification of upward or downward trends.
- Data Visualization Techniques: Employ appropriate data visualization techniques (e.g., bar charts, line graphs, and pie charts) to effectively communicate the cost reduction data.
- Interactive Features: Include interactive features to allow users to drill down into specific data points and explore detailed information.
- User-Friendly Interface: Design the dashboard with a user-friendly interface to ensure easy access and comprehension of the data.
Case Studies in Cost Reduction
Strategic cost management isn’t just about cutting costs; it’s about optimizing resource allocation and achieving sustainable profitability. Real-world examples demonstrate how companies can leverage various strategies to achieve significant cost reductions without sacrificing quality or innovation. These case studies provide valuable insights for organizations looking to improve their cost management practices.Companies across diverse industries have successfully implemented strategic cost management practices, resulting in substantial cost reductions and improved financial performance.
Examining these successful case studies offers practical lessons and actionable strategies for other organizations seeking to optimize their cost structure.
Examples of Successful Cost Reduction Initiatives
Several companies have demonstrated impressive cost reduction through strategic initiatives. Understanding their methods and outcomes provides valuable insights into the practical application of cost management principles.
Company | Industry | Strategies | Results |
---|---|---|---|
Amazon | E-commerce |
|
|
Walmart | Retail |
|
|
Microsoft | Technology |
|
|
Detailed Insights into Successful Strategies
The success stories presented above highlight the diverse range of strategies companies employ to reduce costs. The strategies typically involve a combination of process improvement, technology adoption, and strategic partnerships. Careful analysis of these case studies can reveal patterns and best practices that can be applied to other organizations. A common theme is the importance of data-driven decision making in identifying cost reduction opportunities.
Technology and Tools for Cost Management
Embracing technology is no longer a luxury but a necessity for effective cost management in today’s dynamic business environment. Modern tools provide a powerful arsenal for streamlining processes, optimizing resource allocation, and achieving significant cost reductions. By leveraging the capabilities of software and data analytics, companies can gain actionable insights, automate tasks, and ultimately enhance their bottom line.
Harnessing Technology for Process Improvement
Technology empowers cost management by automating repetitive tasks, streamlining workflows, and enabling real-time monitoring. For example, automated invoice processing software can reduce errors and significantly shorten the time to payment, freeing up valuable staff time for more strategic initiatives. Similarly, project management software facilitates better resource allocation, leading to optimized utilization and decreased project overhead. Advanced analytics tools allow for in-depth examination of cost drivers, enabling proactive measures to mitigate risks and minimize waste.
Software Solutions for Cost Reduction
Software solutions are increasingly crucial for cost reduction efforts. They offer a comprehensive suite of tools to track expenses, analyze spending patterns, and identify areas for improvement. These tools often include budgeting capabilities, expense reporting modules, and dashboards for monitoring performance against targets. The right software can facilitate real-time visibility into costs, enabling proactive adjustments and swift responses to emerging challenges.
Data Analytics for Strategic Cost Management
Data analytics tools are instrumental in uncovering hidden cost savings opportunities. By analyzing large datasets, companies can identify patterns, trends, and anomalies in spending. For example, machine learning algorithms can predict future expenses with greater accuracy, allowing for proactive adjustments and mitigating potential cost overruns. Data visualization tools can translate complex data into easily understandable insights, making it easier for stakeholders to comprehend the impact of cost reduction strategies.
Specific Cost Management Software Benefits
Implementing cost management software brings numerous benefits. Firstly, it automates manual processes, reducing errors and freeing up staff time for higher-value tasks. Secondly, real-time data analysis empowers proactive decision-making. Finally, improved visibility into cost structures facilitates identification of areas for optimization and helps maintain a tight grip on expenditures. These factors contribute to a more efficient and cost-effective business operation.
Cost Management Software Solutions
Software Solution | Key Features | Potential Cost Savings |
---|---|---|
Xero | Accounting, invoicing, expense tracking, reporting | Automated processes reduce errors, streamline payments |
Oracle Cloud Financials | Comprehensive financial management, budgeting, forecasting, analytics | Improved accuracy in budgeting, proactive cost control |
SAP S/4HANA | Integrated ERP system with advanced cost accounting capabilities | Optimized resource allocation, real-time cost visibility |
Zoho Books | Invoicing, expense management, accounting | Streamlined workflow, accurate expense tracking |
Implementing the right cost management software can yield substantial financial returns and enhance the overall efficiency of a business.
Budgeting and Forecasting for Cost Management
Budgeting and forecasting are crucial components of any successful cost management strategy. They provide a framework for planning, tracking, and controlling expenses, enabling organizations to identify potential cost savings and proactively adjust to changing market conditions. By integrating budgeting and forecasting into the cost management process, companies can make informed decisions, optimize resource allocation, and achieve greater financial stability.Budgeting and forecasting are powerful tools for cost reduction.
Get the entire information you require about cima ethics confidentiality rules on this page.
They allow businesses to anticipate future expenses, identify areas where costs can be cut, and implement strategies to achieve those reductions. This proactive approach, rather than simply reacting to unexpected costs, is essential for long-term cost efficiency.
Budgeting with Cost Reduction Targets
Effective budgeting involves integrating cost reduction targets into the overall budget plan. This necessitates a thorough analysis of existing expenses and identification of potential areas for savings. These targets are not arbitrary; they should be based on realistic assessments of current performance and projected future needs.
- Detailed Expense Analysis: A comprehensive review of past spending patterns is critical. Identify areas where expenses are consistently high or fluctuating. This should include not just direct costs but also indirect costs like administrative expenses.
- Realistic Cost Reduction Targets: Set specific, measurable, achievable, relevant, and time-bound (SMART) cost reduction targets. Avoid overly ambitious goals that are unrealistic and might demotivate the team.
- Integration into the Budget: Embed the cost reduction targets directly into the budget. This ensures that the targets are considered in every aspect of the budget, from resource allocation to expense management.
Flexible Budgeting for Adapting to Market Conditions
A static budget, while simple, can quickly become outdated and ineffective in dynamic market environments. A flexible budget, in contrast, is designed to adjust to changing circumstances. This adaptability is vital for businesses facing fluctuating sales, material price changes, or other market volatility.
- Variable Costs: Identify which costs are variable (dependent on production volume or sales) and which are fixed (independent of production volume or sales). Separate these into different sections within the budget to allow for easier adjustments.
- Sensitivity Analysis: Use sensitivity analysis to determine how changes in key variables (like sales volume or raw material costs) affect the overall budget. This provides insights into the potential impact of different market scenarios.
- Scenario Planning: Develop various scenarios reflecting different market possibilities (e.g., optimistic, pessimistic, most likely). This allows for a range of flexible budgets, each representing a specific market condition.
Forecasting Cost Savings Based on Scenarios
Forecasting potential cost savings requires careful consideration of different market scenarios. A thorough analysis of past trends, market forecasts, and anticipated changes in operational processes can help generate reliable cost savings projections.
- Historical Data Analysis: Examine historical cost data to identify patterns and trends. This provides a baseline for understanding cost behavior and potential future savings.
- Market Research: Utilize market research to anticipate changes in raw material costs, labor rates, or other relevant factors. This helps create realistic cost saving projections.
- Implementation of Cost Reduction Strategies: Quantify the potential cost savings associated with specific cost reduction strategies. This may involve using models or simulations to estimate the impact of these strategies.
Sample Budget Incorporating Cost Reduction Targets
A sample budget incorporating cost reduction targets might include specific targets for reducing energy consumption, streamlining supply chain processes, or optimizing employee training programs. These targets should be clearly defined and measurable.
Expense Category | 2023 Budget | 2024 Budget (with Targets) | Projected Cost Savings |
---|---|---|---|
Raw Materials | $100,000 | $90,000 | $10,000 |
Labor | $50,000 | $45,000 | $5,000 |
Utilities | $20,000 | $18,000 | $2,000 |
Total | $170,000 | $153,000 | $17,000 |
Risk Management in Cost Reduction
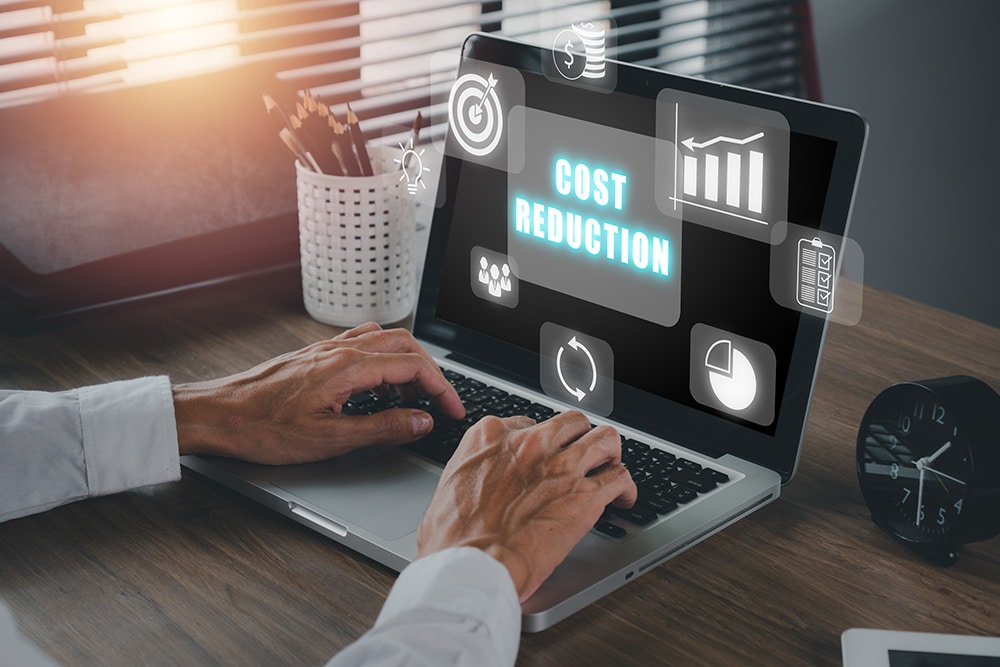
Cost reduction initiatives, while crucial for profitability, often carry inherent risks. Ignoring these potential pitfalls can lead to unexpected expenses, project delays, and ultimately, failure to achieve the desired cost savings. Proactive risk management is therefore essential to navigating the complexities of cost reduction strategies and ensuring their success.Identifying and mitigating potential risks associated with cost reduction is a critical aspect of successful strategic cost management.
Thorough planning, realistic assessments, and contingency measures are essential to minimize negative impacts and maximize the chances of achieving cost savings targets.
Identifying Potential Risks
Cost reduction projects, by their very nature, often involve changes to existing processes, workflows, or personnel. These changes can create unforeseen issues and disrupt the normal operational flow. Understanding the potential sources of risk is the first step in mitigating them.
- Loss of productivity due to unfamiliar processes or inadequate training.
- Reduced quality of output if cost-cutting measures compromise standards.
- Resistance from employees if changes are perceived as unfair or unnecessary.
- Increased customer dissatisfaction if reduced service levels result from cost-cutting.
- Supply chain disruptions if sourcing changes lead to delays or higher costs.
Examples of Unforeseen Issues, Strategic cost management reducing expenses
Several unforeseen issues can derail cost reduction efforts. For instance, a company might decide to outsource a function to reduce labor costs. However, the chosen vendor might prove unreliable, leading to delays in project timelines and unexpected expenses related to quality control and communication. Another example is replacing expensive equipment with cheaper alternatives. The cheaper alternative might prove less efficient in the long run, leading to increased maintenance costs and lower productivity.
Strategies for Managing and Preventing Risks
Proactive risk management strategies can minimize the impact of potential issues. These strategies involve thorough planning, communication, and contingency measures.
- Conduct thorough risk assessments: Identify potential risks associated with each cost-reduction initiative and analyze their likelihood and potential impact. Document these assessments meticulously.
- Develop mitigation strategies: Create specific plans to address each identified risk. These plans should Artikel the actions to be taken if a risk materializes.
- Establish clear communication channels: Keep all stakeholders informed about the cost reduction plan, including the potential risks and mitigation strategies. This fosters buy-in and reduces resistance.
- Implement robust monitoring and evaluation systems: Track the progress of the cost reduction initiative and monitor for any emerging risks. Regular reviews and adjustments to the plan are essential.
- Build in flexibility and contingency plans: Anticipate potential problems and create alternative courses of action to minimize disruptions if unforeseen issues arise.
Risk Assessment Table
A structured approach to risk assessment can significantly improve the success of cost reduction projects. The table below demonstrates a framework for identifying, evaluating, and mitigating potential risks.
Risk Description | Impact | Likelihood | Mitigation Strategy |
---|---|---|---|
Vendor Reliability | Project delays, quality issues, increased costs | Medium | Thorough vendor selection process, backup vendors, contracts with penalties for non-performance. |
Employee Morale | Reduced productivity, increased absenteeism, high turnover | High | Transparent communication, training programs, performance recognition, employee involvement in decision-making. |
Supply Chain Disruptions | Inventory shortages, production delays, increased costs | Medium | Diversification of suppliers, contingency stock, robust supply chain communication channels. |
Reduced Quality | Customer dissatisfaction, warranty claims, reputational damage | Low | Maintain quality standards, rigorous testing procedures, process improvement. |
Sustainability and Cost Management
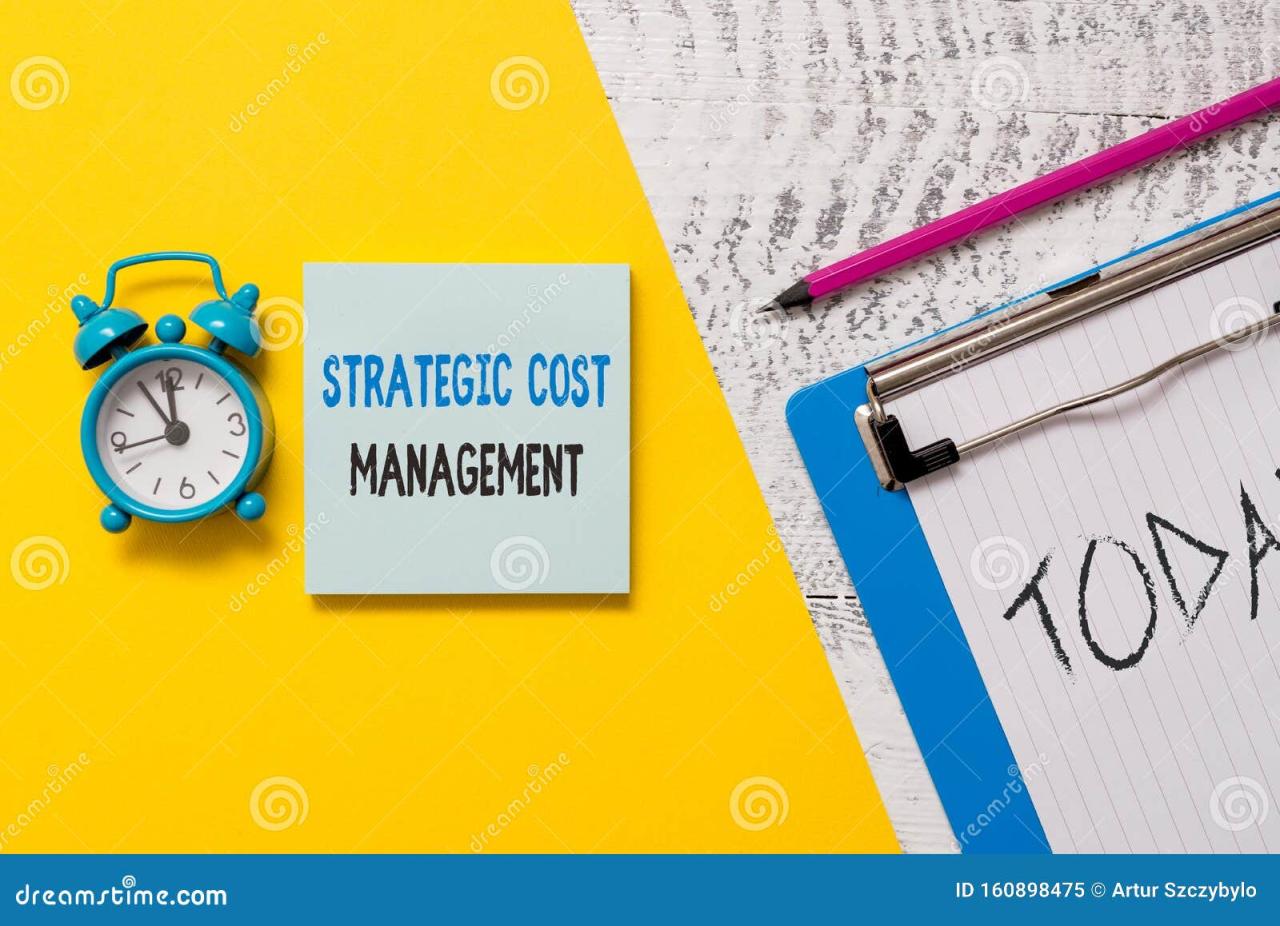
Embracing sustainability isn’t just about doing the right thing for the environment; it’s increasingly a crucial aspect of sound cost management. Companies are realizing that environmentally friendly practices can often lead to significant long-term savings, improving profitability and brand image. This approach shifts the focus from short-term cost cuts to a more holistic strategy that considers the entire lifecycle of products and operations.Sustainable practices aren’t always expensive upfront; often, they represent a shift in mindset and operational efficiency.
By incorporating sustainability considerations into the core cost management strategy, companies can reduce their environmental footprint while simultaneously enhancing their bottom line.
Relationship Between Sustainability and Cost Reduction
Sustainable practices often reduce costs in various ways. Minimizing waste through efficient resource management directly translates to lower material and disposal costs. Energy conservation measures, like implementing renewable energy sources or improving energy efficiency in facilities, can significantly decrease utility expenses. Sustainable procurement, focusing on ethically sourced materials and products with lower environmental impact, can also reduce costs in the long run.
Examples of Environmentally Friendly Practices Leading to Cost Savings
Implementing energy-efficient lighting systems, such as LED lighting, can substantially reduce energy consumption and electricity bills. Adopting a “reduce, reuse, recycle” program for office supplies and waste materials can decrease disposal costs and stimulate creativity in finding new uses for materials. Using recycled or sustainably sourced materials in manufacturing processes can lower material costs and improve the company’s image.
Investing in water conservation technologies, such as low-flow faucets and efficient irrigation systems, can reduce water bills and protect water resources.
How Sustainability Considerations Improve Cost Management Strategy
Incorporating sustainability considerations into a company’s cost management strategy can lead to significant improvements. A focus on resource efficiency and waste reduction translates into lower operating costs. Sustainable procurement practices can lead to more stable and predictable supply chains, mitigating risks associated with volatile material prices. Furthermore, a commitment to sustainability often attracts environmentally conscious customers, leading to increased brand loyalty and potentially higher revenue streams.
By integrating sustainability into the core business strategy, companies can build resilience and reduce long-term operational risks.
Traditional Cost-Cutting Measures vs. Sustainable Alternatives
Traditional Cost-Cutting Measures | Sustainable Alternatives |
---|---|
Layoffs, reduced staff | Process optimization, training, automation to improve efficiency without reducing staff. |
Cutting maintenance budgets | Investing in preventative maintenance programs to reduce unexpected breakdowns and associated costs. |
Reducing quality control | Implementing robust quality control systems to reduce waste and defects during production. |
Using cheaper, less durable materials | Using recycled or sustainably sourced materials, prioritizing durability over cost. |
Ignoring waste management | Implementing comprehensive waste management programs including recycling and reuse initiatives. |
Summary
In conclusion, strategic cost management reducing expenses is a multifaceted process requiring careful planning, execution, and evaluation. By understanding the core principles, identifying opportunities, and implementing effective strategies, businesses can achieve significant cost savings while simultaneously improving operational efficiency and overall performance. The key takeaway is that a strategic approach to cost reduction is essential for long-term success.